Optimizing UAV Wing Performance: A Computational Analysis with Computer-Based Algorithms for Composite Material Integration
Keywords:
Wing, FEM, Composite materials, Structural Analysis, Weight reductionAbstract
Introduction/Importance of Study: The aircraft wing, a vital component, demands intricate design to balance lift generation, drag reduction, and weight minimization. In advanced UAVs (Unmanned Aerial Vehicles), prioritizing stealth and low weight, a pioneering solution involves replacing traditional metallic wing components with composite materials, offering superior lightweight properties, strength, durability, and flexibility.
Novelty Statement: Since most of the studies focus on fuselage, wing ribs, and skin, this research emphasizes spars which are a primary component of the wing.
Material and Method: Composite material T800S/3900-2 is a widely used carbon fiber material in the aerospace industry, which is proposed to be utilized in wing spars. The finite element method is used to carry out the investigation and verification of this transition of materials from metals to composite materials.
Result and Discussion: By varying ply orientations and thicknesses of composite materials to match the stiffness and strength of metal spars, our findings demonstrate that composite wing spars exhibit equivalent stiffness, greater strength, and reduced weight compared to traditional metallic counterparts.
Concluding Remarks: The shift to composite materials in UAV wing design offers a transformative solution. This research shows that for optimal structural performance and achieving lower weight objective composite materials, composite materials are the most suitable materials for UAV wing spars.
References
C. Soutis, “Aerospace engineering requirements in building with composites,” Polym. Compos. Aerosp. Ind., pp. 3–22, Jan. 2020, doi: 10.1016/B978-0-08-102679-3.00001-0.
V. R. A. Prakash, M. Bourchak, H. Alshahrani, and K. A. Juhany, “Synthesis and characterization of lightweight unmanned aerial vehicle composite building material for defense application,” Biomass Convers. Biorefinery, pp. 1–12, Aug. 2023, doi: 10.1007/S13399-023-04736-2/METRICS.
N. Mazlan, T. Chai Hua, S. M. Sapuan, and R. A. Ilyas, “Evolution of Aerospace Composite Materials,” Adv. Compos. Aerosp. Eng. Appl., pp. 367–385, Jan. 2022, doi: 10.1007/978-3-030-88192-4_18/COVER.
M. Bhong et al., “Review of composite materials and applications,” Mater. Today Proc., Oct. 2023, doi: 10.1016/J.MATPR.2023.10.026.
S. B. Nagaraju, H. C. Priya, Y. G. T. Girijappa, and M. Puttegowda, “Lightweight and sustainable materials for aerospace applications,” Light. Sustain. Compos. Mater. Prep. Prop. Appl., pp. 157–178, Jan. 2023, doi: 10.1016/B978-0-323-95189-0.00007-X.
A. Marius, “General principles of passive radar signature reducing-stealth technology and its applications”, doi: 10.13111/2066-8201.2010.2.1.6.
C. Xu et al., “Application of Carbon Composites in Unmanned Aerial Vehicles: A Review,” Lect. Notes Electr. Eng., vol. 861 LNEE, pp. 3479–3485, 2022, doi: 10.1007/978-981-16-9492-9_343/COVER.
B. Szabó and I. Babuška, “Finite Element Analysis: Method, Verification and Validation, Second Edition,” Finite Elem. Anal. Method, Verif. Validation, Second Ed., pp. 1–363, Jan. 2021, doi: 10.1002/9781119426479.
W. K. Liu, S. Li, and H. S. Park, “Eighty Years of the Finite Element Method: Birth, Evolution, and Future,” Arch. Comput. Methods Eng. 2022 296, vol. 29, no. 6, pp. 4431–4453, Jun. 2022, doi: 10.1007/S11831-022-09740-9.
S. A. Ardila-Parra, C. M. Pappalardo, O. A. G. Estrada, and D. Guida, “Finite Element based Redesign and Optimization of Aircraft Structural Components using Composite Materials,” IAENG Int. J. Appl. Math., Dec. 2020, Accessed: Mar. 13, 2024. [Online]. Available: https://hal.science/hal-03020637
S. D. Müzel, E. P. Bonhin, N. M. Guimarães, and E. S. Guidi, “Application of the Finite Element Method in the Analysis of Composite Materials: A Review,” Polym. 2020, Vol. 12, Page 818, vol. 12, no. 4, p. 818, Apr. 2020, doi: 10.3390/POLYM12040818.
F. Mazhar and A. M. Khan, “Structural design of a UAV wing using finite element method,” Collect. Tech. Pap. - AIAA/ASME/ASCE/AHS/ASC Struct. Struct. Dyn. Mater. Conf., 2010, doi: 10.2514/6.2010-3099.
K. Raja Sekar, M. Ramesh, R. Naveen, M. S. Prasath, and D. Vigneshmoorthy, “Aerodynamic design and structural optimization of a wing for an Unmanned Aerial Vehicle (UAV),” IOP Conf. Ser. Mater. Sci. Eng., vol. 764, no. 1, p. 012058, Feb. 2020, doi: 10.1088/1757-899X/764/1/012058.
M. A. Khan et al., “A Study on Flight Time Enhancement of Unmanned Aerial Vehicles (UAVs) Using Supercapacitor-Based Hybrid Electric Propulsion System (HEPS),” Arab. J. Sci. Eng., vol. 46, no. 2, pp. 1179–1198, Feb. 2021, doi: 10.1007/S13369-020-04941-5/METRICS.
S. Guo, “Aeroelastic optimization of an aerobatic aircraft wing structure,” Aerosp. Sci. Technol., vol. 11, no. 5, pp. 396–404, Jun. 2007, doi: 10.1016/J.AST.2007.01.003.
N. Z. Zaki et al., “Effect of Skin and Spar Laminate Orientations on Flutter of Composite UAV Wing,” J. Aeronaut. Astronaut. Aviat., vol. 51, no. 2, pp. 201–211, Jun. 2019, doi: 10.6125/JOAAA.201906_51(2).05.
K. K. Rumayshah, A. Prayoga, and M. Agoes Moelyadi, “Design of High Altitude Long Endurance UAV: Structural Analysis of Composite Wing using Finite Element Method,” J. Phys. Conf. Ser., vol. 1005, no. 1, p. 012025, Apr. 2018, doi: 10.1088/1742-6596/1005/1/012025.
O. A. Adeleke, G. E. Abbe, P. O. Jemitola, and S. Thomas, “Design of the Wing of a Medium Altitude Long Endurance UAV,” Int. J. Eng. Manuf., vol. 12, no. 1, p. 37, Feb. 2022, doi: 10.5815/IJEM.2022.01.04.
E. Valot and P. Vannucci, “Some exact solutions for fully orthotropic laminates,” Compos. Struct., vol. 69, no. 2, pp. 157–166, Jul. 2005, doi: 10.1016/J.COMPSTRUCT.2004.06.007.
A. Vincenti, P. Vannucci, and G. Verchery, “Influence of orientation errors on quasi-homogeneity of composite laminates,” Compos. Sci. Technol., vol. 63, no. 5, pp. 739–749, Apr. 2003, doi: 10.1016/S0266-3538(02)00263-4.
A. Puck and H. Schürmann, “Failure analysis of FRP laminates by means of physically based phenomenological models,” Fail. Criteria Fibre-Reinforced-Polymer Compos., pp. 832–876, Jan. 2004, doi: 10.1016/B978-008044475-8/50028-7.
E. I. Basri et al., “Performance analysis of composite ply orientation in aeronautical application of unmanned aerial vehicle (UAV) NACA4415 wing,” J. Mater. Res. Technol., vol. 8, no. 5, pp. 3822–3834, Sep. 2019, doi: 10.1016/J.JMRT.2019.06.044.
E. Sarmiento, C. Díaz-Campoverde, J. Rivera, C. Cruzatty, E. Cando, and E. Valencia, “Aero-structural numerical analysis of a blended wing body unmanned aerial vehicle using a jute-based composite material,” Mater. Today Proc., vol. 49, pp. 50–57, Jan. 2022, doi: 10.1016/J.MATPR.2021.07.470.
K. Naresh, S. Krishnapillai, and V. Ramachandran, “Effect of Fiber Orientation on Carbon/Epoxy and Glass/Epoxy Composites Subjected to Shear and Bending,” Solid State Phenom., vol. 267, pp. 103–108, 2017, doi: 10.4028/WWW.SCIENTIFIC.NET/SSP.267.103.
L. Ünlüsoy, “Structural design and analysis of the mission adaptive wings of an unmanned aerial vehicle,” 2010, Accessed: Mar. 13, 2024. [Online]. Available: https://open.metu.edu.tr/handle/11511/19160
and J. H. C. S. Gi, D. Kumar, Y. Park, J.H. KweonJ.H, “Structural Design and Analysis of Composite Aircraft Fuselage Used to Develop AFP Technology,” 2013.
G. R. Liu and S. S. Quek, “The Finite Element Method: A Practical Course: Second Edition,” Finite Elem. Method A Pract. Course Second Ed., pp. 1–433, 2013, doi: 10.1016/C2012-0-00779-X.
G. Kanesan, S. Mansor, and A. Abdul-Latif, “Validation of UAV wing structural model for finite element analysis,” J. Teknol., vol. 71, no. 2, pp. 1–5, 2014, doi: 10.11113/JT.V71.3710.
V. Giurgiutiu, “Structural health monitoring (SHM) of aerospace composites,” Polym. Compos. Aerosp. Ind., pp. 449–507, Jan. 2015, doi: 10.1016/B978-0-85709-523-7.00016-5.
C. B. York, “On Bending-Twisting coupled laminates,” Compos. Struct., vol. 160, pp. 887–900, Jan. 2017, doi: 10.1016/J.COMPSTRUCT.2016.10.063.
D. Cui and D. Li, “Bending-twisting coupled structures based on composite laminates with extension-shear coupling effect,” Compos. Struct., vol. 209, pp. 434–442, Feb. 2019, doi: 10.1016/J.COMPSTRUCT.2018.09.095.
R. E. Murray, D. A. Doman, and M. J. Pegg, “Finite element modeling and effects of material uncertainties in a composite laminate with bend–twist coupling,” Compos. Struct., vol. 121, pp. 362–376, Mar. 2015, doi: 10.1016/J.COMPSTRUCT.2014.11.035.
“How to read representations of pressure around an airfoil? - Aviation Stack Exchange.” Accessed: Mar. 13, 2024. [Online]. Available: https://aviation.stackexchange.com/questions/33450/how-to-read-representations-of-pressure-around-an-airfoil
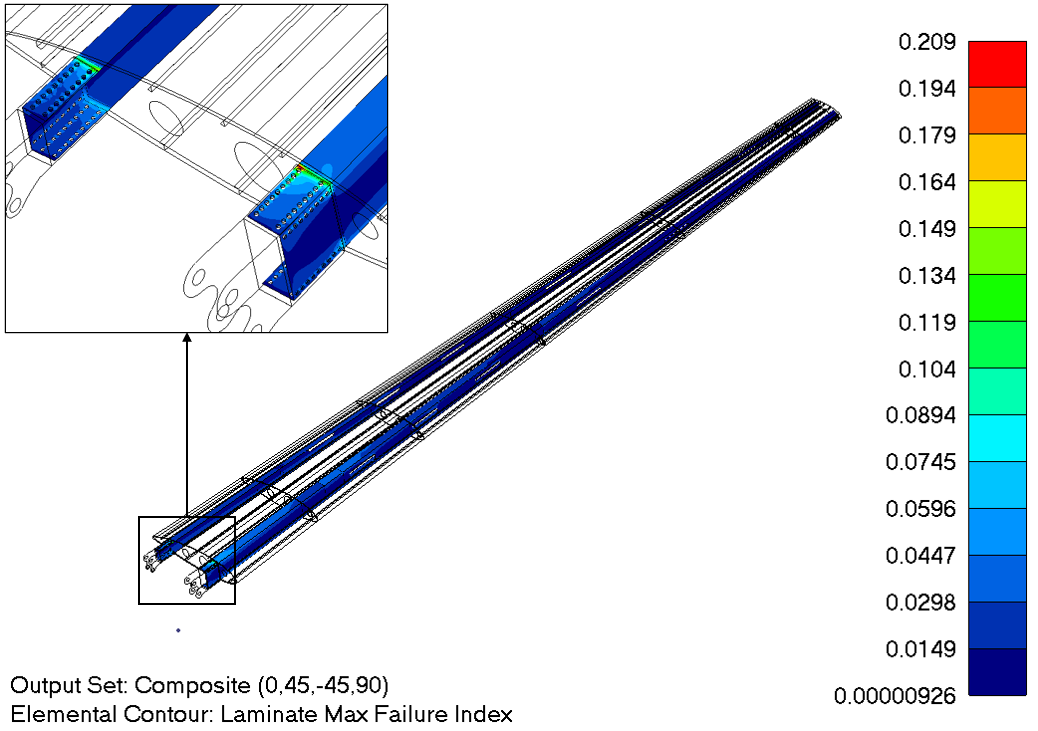
Published
How to Cite
Issue
Section
License
Copyright (c) 2024 50SEA

This work is licensed under a Creative Commons Attribution 4.0 International License.