A Qualified review on ML and DL algorithms for Bearing Fault Diagnosis
Keywords:
Ball Bearing, Feature Engineering, Repetitive Neural Network, Generative model as Adversarial Network, Convolutional neural networkAbstract
Moving machinery is the backbone of socio-economic development. The use of machines help in increasing the production of everyday used items, and tools, that generate electricity and mechanical energy, and provides easy and fast transportation and help by saving human efforts, energy, and time. The mechanical industry is totally dependent on the bearing and it is considered as bread and butter of the system. Bearing failure is about 40% of the total failures of induction motors which is why it is a crucial challenge to predict the failure and helps prevent future downtime events through maintenance schedules with the latest techniques and tools of. This paper presents a review of how DL techniques and algorithms outsmarted ML for bearing fault detection and diagnosis and summarizes the accuracy results generated by most common DL algorithms over classical ML algorithms.Additionally this paper reasons different criteria for which DL algorithms have been proved efficient for building productive model in the field of bearing fault detection. Furthermore, some of the most famous datasets by different universities have been discussed and accuracy results are provided by reviewing algorithms on the CWRU dataset by different researchers and comparison chart is listed in the results section.
References
“Report of large motor reliability survey of industrial and commercial installations, Part I,” IEEE Trans. Ind. Appl., vol. IA–21, no. 4, pp. 853-864, Jul./Aug. 1985.
“Report of large motor reliability survey of industrial and commercial installations, Part II,” IEEE Trans. Ind. Appl., vol. IA–22, no. 4, pp. 865–872, Jul./Aug. 1985.
K. Teotrakool, M. J. Devaney and L. Eren, “Bearing fault detection in adjustable speed drives via a support vector machine with feature selection using a genetic algorithm,” in Proc. IEEE Instrum. Mea. Technol. Conf., Victoria, BC, Canada, 2008, pp. 1129–1133.
Soft Comput., vol. 11, no. 6, pp. 4203–4211, Sep. 2011. [51] T. Benkedjouh, K. Medjaher, N. Zerhouni and S. Rechak, “Fault prognostic of bearings by using support vector data description,” in Proc. IEEE Conf. Progno. Health Manag., Denver, CO, USA, 2012, pp. 1–7.
(PHM), Beijing, China, 2017, pp. 1–5. [57] B. R. Nayana and P. Geethanjali, “Analysis of statistical time-domain features effectiveness in identification of bearing faults from vibration signal,” IEEE Sensors J., vol. 17, no. 17, pp. 5618–5625, 1 Sept.1, 2017.
M. Cococcioni, B. Lazzerini and S. L. Volpi, “Robust diagnosis of rolling element bearings based on classification techniques,” IEEE Trans. Ind. Informat., vol. 9, no. 4, pp. 2256–2263, Nov. 2013.
A. Widodo, D. Satrijo, T. Prahasto, G.-M. Lim, and B.-K. Choi, “Confirmation of Thermal Images and Vibration Signals for Intelligent Machine Fault Diagnostics,” International Journal of Rotating Machinery, vol. 2012, pp. 1–10, 2012.
G.-m. Lim, Y. Ali, and B.-s. Yang, “The Fault Diagnosis and Monitoring of Rotating Machines by Thermography,” in Engineering Asset Man- agreement and Infrastructure Sustainability, J. Mathew, L. Ma, A. Tan, M. Weijnen, and J. Lee, Eds. Springer London, 2012, pp. 557–565.
C. J. C. Burges, “A tutorial on support vector machines for pattern recognition,” Data Mining and Knowledge Discovery, vol. 2, pp. 1–43, 1998.
P. Nectoux et al., “Pronostia: An experimental platform for bearings accelerated life test, in Proc. IEEE Int. Conf. Prognostics Health Manag., Denver, CO, USA, 2012, pp. 18.
W. Mao, Y. Liu, L. Ding and Y. Li, “Imbalanced fault diagnosis of rolling bearing based on generative adversarial network: A comparative study,” IEEE Access, vol. 7, pp. 9515–9530, 2019
S. Suh, H. Lee, J. Jo, P. Lukowicz, and Y.-Oh Lee, “Generative Oversampling Method for Imbalanced Data on Bearing Fault Detection and Diagnosis”, Appl. Sci., vol. 9, no. 4, 746, 2019
Liu, H., Motoda H. (1998) Feature Selection for Knowledge Discovery and Data MiningFeature Selection for Knowledge Discovery and Data Mining., Kluwer Academic Publishers. Norwell, MA, USA. 1998
"Feature engineering in Machine Learning" (PDF). Zdenek Zabokrtsky. Archived from the original (PDF) on 4 March 2016. Retrieved 12 November 2015
S. Zhang, S. Zhang, B. Wang and T. G. Habetler, “Deep Learning Algorithms for Bearing Fault Diagnostics - A Review,” in Proc. IEEE Int. Symp. Diagnostics Electr. Mach., Power Electron. Drives, Toulouse, France, 2019, pp. 257-263.
Martin Arjovsky, Amar Shah, and Yoshua Bengio. Unitary evolution recurrent neural networks. In International Conference on Machine Learning, pages 1120–1128, 2016.
Liu Buyu. Study on Rolling Bearing Fault Diagnosis Based on Deep Learning. Hangzhou Dianzi University, 2019.
M. Cerrada et al., “A review on data-driven fault severity assessment in rolling bearings,” Mech. Syst. Signal Process., vol. 99, pp. 169–196, Jan. 2018.
J. Lee, H. Qiu, G. Yu, J. Lin, and Rexnord Technical Services, IMS, University of Cincinnati. “Bearing Data Set” NASA Ames Prognostics Data Repository, NASA Ames Research Center, Moffett Field, CA, Accessed: Jul. 2019, [Online]. Available: http://ti.arc.nasa.gov/project/prognostic-data-repository.
A. Zappone, M. Di Renzo, and M. Debbah, “Wireless Networks Design in the Era of Deep Learning: Model-Based, AI-Based, or Both?,” IEEE Trans. Commun., vol. 67, no. 10, pp. 7331–7376, Oct. 2019.
M. Xia, T. Li, L. Xu, L. Liu and C. W. de Silva, “Fault diagnosis for rotating machinery using multiple sensors and convolutional neural networks,” IEEE/ASME Trans. Mechatronics, vol. 23, no. 1, pp. 101– 110, Feb. 2018.
Z. Zhuang and Q. Wei, “Intelligent fault diagnosis of rolling bearing using one-dimensional multi-scale deep convolutional neural network based health state classification,” in Proc. 2018 IEEE 15th Int. Conf. Netw., Sens. & Control (ICNSC), Zhuhai, China, 2018, pp. 1–6.
W. Zhang, C. Li, G. Peng, Y. Chen, Z. Zhang, “A deep convolutional neural network with new training methods for bearing fault diagnosis under noisy environment and different working load,” Mech. Syst. Signal Process., vol. 100, pp. 439–458, 2018.
R. Liu, G. Meng, B. Yang, C. Sun and X. Chen, “Dislocated time series convolutional neural architecture: An intelligent fault diagnosis approach for electric machine,”
no. 3, pp. 1310–1320, June 2017. [107] C. Lu, Z. Wang, and Bo Zhou, “Intelligent fault diagnosis of rolling bearing using hierarchical convolutional network-based health state classification,” Adv. Eng. Informat., vol. 32, pp. 139–157, 2017.
W. Abed, S. Sharma, R. Sutton, and A. Motwani, “A robust bearing fault detection and diagnosis technique for brushless DC motors under non-stationary operating conditions,” J. Control Autom. Electr. Syst., vol. 26, no. 3, pp. 241–254, Jun. 2015.
L. Guo, N. Li, F. Jia, Y. Lei, and J. Lin, “A recurrent neural network based health indicator for remaining useful life prediction of bearings,” Neurocomput., vol. 240, pp. 98–109, 2017.
Y. O. Lee, J. Jo and J. Hwang, “Application of deep neural network and generative adversarial network to industrial maintenance: A case study of induction motor fault detection,” in Proc. IEEE Int. Conf. Big Data, Boston, MA, 2017, pp. 3248–3253.
A. Radford, L. Metz, and S. Chintala, “Unsupervised representation learning with deep convolutional generative adversarial networks,” arXiv preprint arXiv:1511.06434, 2015.
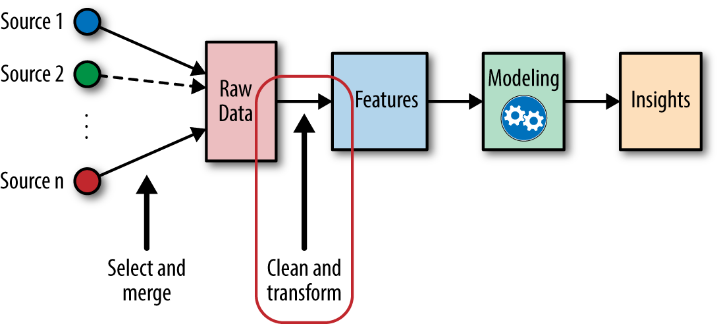
Published
How to Cite
Issue
Section
License
Copyright (c) 2022 50SEA

This work is licensed under a Creative Commons Attribution 4.0 International License.